Step 01
Casting
Aluminium casting is a manufacturing process where molten aluminium is poured into a mold to create specific shapes and components. It is commonly used for producing complex and precise parts in industries such as automotive, aerospace, and machinery. The process allows for excellent detail, strength, and durability in the finished products. Aluminium casting can be done through various methods like sand casting, die casting, and investment casting, each suited to different requirements of design, volume, and material properties. This technique is valued for its ability to create lightweight yet strong components that are highly resistant to corrosion.
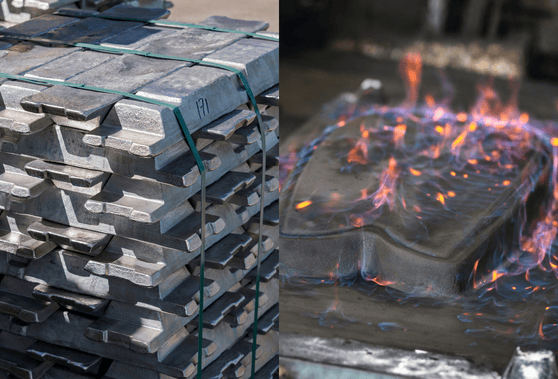
Step 02
Raw Materials
Aluminium is a lightweight, corrosion-resistant metal widely used across various industries. It is known for its flexibility and strength, making it ideal for applications in sectors such as aerospace, automotive, and construction. The raw material for aluminium is typically obtained from bauxite ore, which is then refined through chemical processes to produce aluminium metal. This metal has a distinctive silvery-white appearance and is also renowned for its high conductivity, malleability, and recyclability.
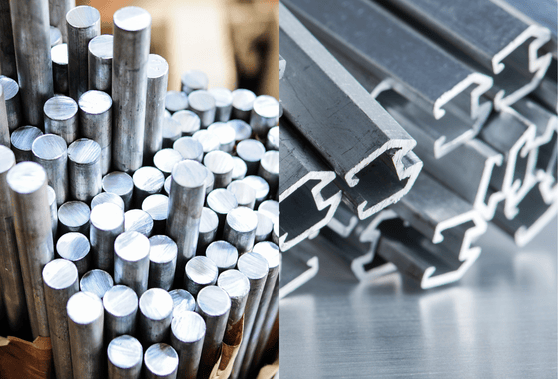
Step 03
Machining
Dhreel And sliding Machin is a machine tool used to machine the turning surface by rotating the workpiece and moving the feed turning tool. According to use: instrument , Dhreel Machin, Hand Sliding Machin, etc.
Drilling machine: This is a machine that mainly uses a drill to process holes on the workpiece. Generally, the bit rotates with the main motion, while the bit moves axially with the feed motion.
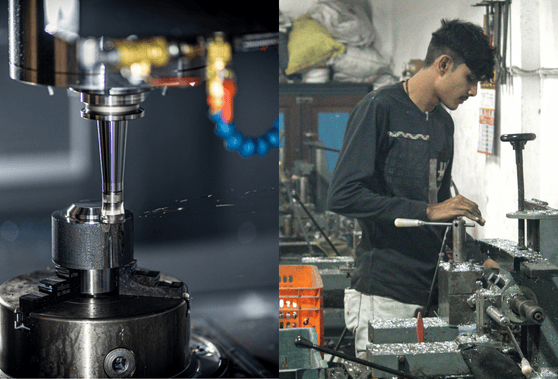
Step 04
Polishing
This process is essential to achieve precise surface finishing. To obtain a high-quality product that exudes a shine, the Aluminium surface is polished to technical precision. This is a combination of manual and machine- driven processes. Once the polishing is done, only then can the product be sent for chrome plating.
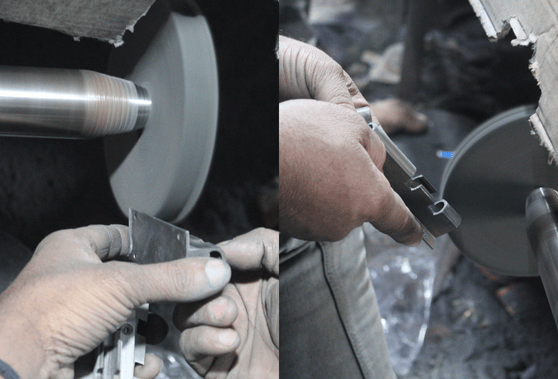
Step 05
Electroplating
In this process, first, a base coating of electroplated Nickel is applied to the product. After that, a thin coating of electroplated chromium is applied. The chromium layer makes it durable and corrosion-resistant.
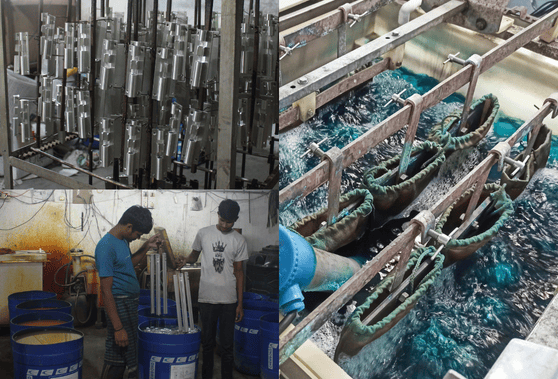
Step 06
Assembly Line
After electroplated and passed the inspection, it can enter the assembly process. Assembly is the process of connecting processed parts in a certain order and technology to become a complete product and reliably realize the function of product design.
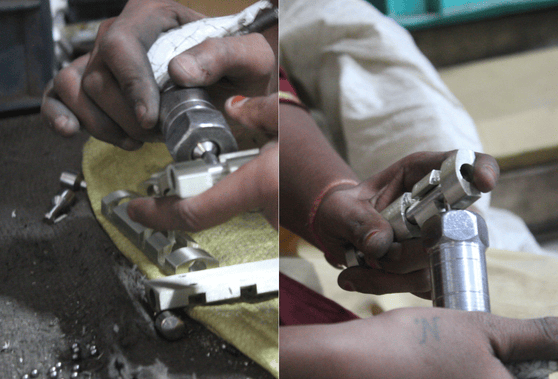
Step 07
Testing
The created Aluminium Tower bolt are then tested rigorously on both Measurement and Finishing. Samples are tested for critical dimensions and durability. Aluminium Tower bolt are also required to pass several environmental regulations.
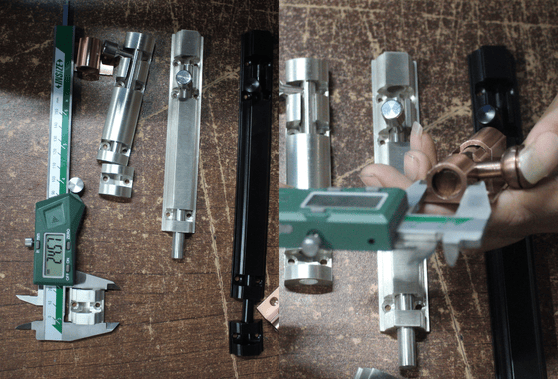
Step 08
Packing & Dispatching
Once the products have been Tested and Shifted to the packing area, packers choose an appropriate box to put the products in. it’s important to use a properly sized box so that we can reduce the amount of wasted space. After Packing Final Product in Small Boxes, Boxes are Packed in Master Cartoon. And Material Ready to Dispatched Or Store.
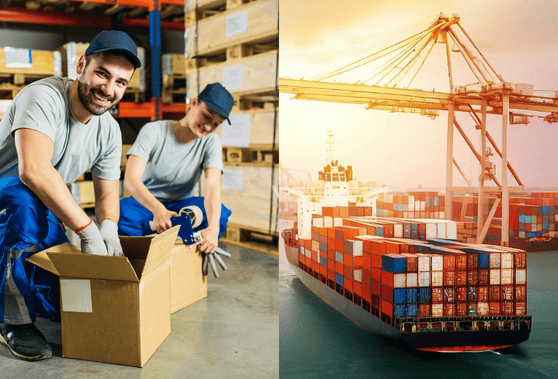